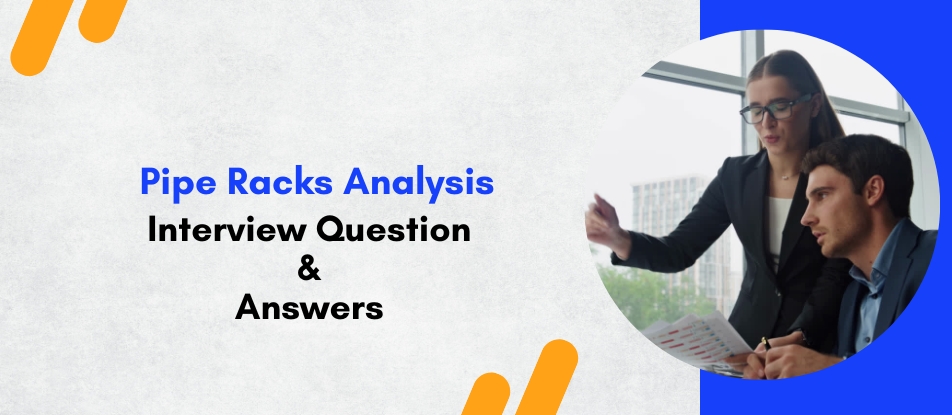
This comprehensive Pipe Racks Analysis course equips engineers with the skills to design, analyze, and evaluate structural pipe rack systems used in process industries. Covering topics such as load distribution, support configurations, thermal expansion, seismic impacts, and multidisciplinary coordination, the course blends theoretical concepts with practical applications. Participants will gain hands-on experience using industry-standard tools to ensure safe, efficient, and compliant pipe rack designs for both greenfield and brownfield projects.
Pipe Racks Analysis Training Interview Questions Answers - For Intermediate
1. What are the typical materials used for constructing pipe racks?
Pipe racks are commonly constructed using structural steel, such as mild steel or hot-rolled sections like I-beams and H-beams. The material is selected based on load-bearing capacity, corrosion resistance, and ease of fabrication, with protective coatings or galvanization often applied for durability.
2. How is load distribution calculated for multi-tier pipe racks?
Load distribution in multi-tier pipe racks is calculated by assessing the cumulative load on each level, including the weight of pipes, insulation, contents, and supports. The loads from upper tiers are transferred to the base and foundation, requiring careful structural analysis to avoid overloading.
3. What challenges are faced in designing pipe racks for brownfield projects?
Brownfield projects often involve space constraints, existing structures, and limited access. Designers must account for previously installed utilities, structural compatibility, and the need to retrofit supports without interrupting plant operations, often requiring laser scanning and detailed field assessments.
4. What is the importance of anchor points in a pipe rack system?
Anchor points restrict axial movement of pipes, allowing controlled thermal expansion and maintaining structural stability. Their placement must be strategic to prevent over-stressing the rack or pipe system, often near fixed equipment or at the start of long runs.
5. What considerations are made for drainage on pipe racks?
Proper slope is provided in piping for fluid drainage, especially for water, steam, or condensate lines. Additionally, the rack itself may be designed with drainage paths or grating to avoid water accumulation, which can cause corrosion or slippage hazards.
6. How are fire safety requirements incorporated in pipe rack design?
Designers must ensure adequate spacing between flammable lines and incorporate fireproof coatings on structural elements. Firefighting access, isolation valves, and drainage systems are integrated, following NFPA standards or local fire safety regulations.
7. What is the significance of modularization in pipe rack design?
Modularization allows pipe rack sections to be fabricated off-site and assembled on-site, improving construction efficiency, reducing on-site labor, and enhancing quality control. It's especially valuable in large or remote projects where site access is limited.
8. How do pipe movements due to pressure affect pipe rack design?
Internal pressure can cause slight axial elongation or ballooning of pipes. While minor, this effect, when combined with thermal expansion, must be considered in stress analysis to avoid excessive force on supports and anchors.
9. What are cable trays, and how do they interact with pipe racks?
Cable trays are support systems for electrical and instrumentation cables and are often mounted on pipe racks. Their placement requires coordination to prevent interference with pipe routing and to maintain separation from heat-emitting lines.
10. Why is vertical clearance important in pipe rack design?
Vertical clearance between pipe tiers ensures safe maintenance access, prevents thermal interaction, and accommodates insulation and supports. Industry standards often specify minimum clearances for different pipe sizes and service categories.
11. How do environmental factors influence pipe rack design?
Environmental factors such as humidity, temperature fluctuations, wind, and seismic activity affect material selection, corrosion protection, and structural bracing. In coastal or chemical environments, anti-corrosion measures like epoxy coatings or stainless steel are used.
12. What documents are essential for pipe rack analysis?
Key documents include piping and instrumentation diagrams (P&IDs), general arrangement drawings (GADs), line lists, load data sheets, stress analysis reports, and structural design specifications. These guide load calculation, support placement, and structural design.
13. How are dynamic loads handled in pipe rack systems?
Dynamic loads from vibrating equipment, surge pressure, or wind gusts are managed through flexible supports, snubbers, and dampers. Dynamic analysis ensures the rack can withstand these loads without resonance or fatigue.
14. What is the impact of support settlement on pipe racks?
Support settlement can lead to uneven load distribution, pipe sagging, or overstressing of connections. It's critical to ensure proper foundation design, soil testing, and allowance for minor adjustments post-installation.
15. How is constructability factored into pipe rack design?
Constructability includes ease of erection, access for welding or bolting, and alignment for modular assembly. Designers must consider transportation limits, crane access, and safe lifting points to ensure efficient and safe installation.
Pipe Racks Analysis Training Interview Questions Answers - For Advanced
1. How do you optimize pipe rack design for cost efficiency without compromising safety or compliance?
Optimizing pipe rack design for cost efficiency involves strategic planning of layout, materials, support spacing, and load management. Standardizing bay lengths and using repetitive structural elements reduces fabrication complexity. Efficient routing minimizes pipe length and support numbers, while avoiding unnecessary elevations cuts steel tonnage. Selecting appropriate materials—such as high-strength low-alloy steel for weight reduction—and using modular fabrication techniques help lower labor costs. At the same time, adherence to safety codes (e.g., ASCE, AISC, IS 800) and sufficient load allowances ensure structural integrity. Early interdisciplinary coordination also prevents costly late-stage modifications and eliminates overdesign caused by unaccounted loads or space requirements.
2. What are the best practices for performing a load take-off for a pipe rack system?
Accurate load take-off begins with gathering data from piping line lists, isometric drawings, and equipment loads. Each pipe’s weight—including content, insulation, and fittings—is calculated per unit length, multiplied by its span. Live loads, wind and seismic forces, and thermal movements are considered as per applicable codes. Special attention is given to concentrated loads from valves or instruments. Load combinations are developed, and results are shared across disciplines to coordinate support placements. Best practices include using software tools like Excel templates or piping design software, verifying assumptions with senior engineers, and revisiting load take-offs as designs evolve to ensure alignment with actual routing.
3. What approach do you take for tier arrangement in multi-level pipe racks?
Tier arrangement in multi-level racks is planned based on process criticality, pipe size, fluid service, and access needs. Heavier and high-temperature lines are typically placed at the lowest level to reduce structural load impact. Instrument air, electrical, and utility lines are placed higher to segregate hazardous services. Adequate vertical clearance is maintained per standards, factoring insulation and maintenance space. Crossovers, valve access, and future expansion are also considered. Using a tier matrix during the planning phase helps visualize the distribution and ensures logical, safe, and maintainable layouts. Consistency across racks in a project also simplifies fabrication and construction.
4. How do you validate the stability of tall pipe racks exposed to strong winds or cyclones?
Tall pipe racks in wind-prone areas are analyzed using wind pressure coefficients from standards like ASCE 7 or IS 875. The pipe and structural members’ exposed areas are calculated for each face, and wind loads are applied to simulate pressure and suction effects. Lateral stability is checked using moment-resisting frames, diagonal bracing, or portal frames. Torsional buckling and uplift are assessed for roof-mounted structures. Foundations are designed with sufficient anchorage or pile systems to resist overturning. Dynamic wind load effects like vortex shedding may require damping systems or increased stiffness. Wind tunnel testing is sometimes conducted for critical structures in cyclone zones.
5. What is the role of guide, stop, and anchor supports on pipe racks, and how do they affect structural loads?
Guide, stop, and anchor supports control pipe movements due to thermal expansion, pressure, and dynamic loads. Anchors restrict all movement and transmit axial and lateral loads to the pipe rack, requiring structural reinforcement. Stops limit axial displacement while allowing lateral and vertical movement, whereas guides permit only longitudinal sliding. Incorrect placement of these supports can overstress structural members or cause pipe system failures. Their locations are determined through pipe stress analysis and influence beam sizing and connection detailing. Load data from Caesar II is used to input reaction forces into structural models, ensuring the frame can safely resist imposed forces.
6. How do you manage pipe rack design changes during late stages of a project?
Managing late-stage design changes involves a systematic change management process, including impact assessment, approval workflows, and interdisciplinary coordination. The first step is identifying whether changes affect routing, load, access, or support configuration. Then, structural and stress analyses are revisited, and updates are propagated to fabrication drawings and BOMs. Delayed changes are logged with revision numbers and justifications. Coordination with procurement, construction, and QA teams ensures changes are implemented consistently. When changes are unavoidable, prefabricated components are reused where possible, and temporary field adjustments are minimized through clear redlining and field engineering support.
7. What are the key considerations when designing pipe racks in offshore or marine environments?
Pipe racks in offshore or marine environments face harsh conditions like salt spray, high winds, wave impacts, and limited maintenance access. Corrosion-resistant materials (e.g., stainless steel, duplex steel) and protective coatings (e.g., epoxy, galvanizing) are essential. Structural design must consider dynamic platform movements, wave loading, and offshore codes like DNV or ISO 19901. Rack layout must optimize weight distribution due to platform load limits. Compact, modular construction is preferred due to limited working space. All bolts and welds are designed for durability in humid, saline conditions, and cathodic protection may be added for submerged elements.
8. Explain how 3D modeling and BIM contribute to effective pipe rack analysis and design.
3D modeling and BIM (Building Information Modeling) enhance pipe rack design by enabling real-time visualization, clash detection, and coordination across disciplines. Software like AVEVA E3D, AutoCAD Plant 3D, or Tekla Structures allows accurate placement of pipes, supports, and structural members. Clash detection prevents interferences with cable trays, HVAC ducts, or equipment. BIM integrates civil, electrical, and mechanical data, ensuring alignment from concept to construction. It also allows simulation of erection sequences and maintenance scenarios. Additionally, 3D models are used to generate fabrication drawings, material take-offs, and digital twins for lifecycle management and maintenance planning.
9. How do live loads such as maintenance and operational activities influence pipe rack design?
Live loads from maintenance activities include the weight of personnel, tools, mobile equipment, and vibrations from operational equipment. Design standards prescribe a uniform live load (typically 2.5–5 kN/m²) on platforms and access walkways. For pipe racks that serve as walkways or support valves and instruments, these loads are added to dead and environmental loads. Concentrated loads from service platforms, mobile trolleys, or access ladders are also considered. Ignoring live loads can compromise safety, so structural members and supports must be adequately sized, and grating, handrails, and ladders must meet OSHA or IS safety standards.
10. What are the main design challenges when pipe racks cross roads or other obstructions?
Crossing roads or obstructions requires pipe racks to span long distances or be elevated to meet clearance requirements. These spans increase bending moments and deflections, requiring deeper beams, trusses, or portal frames. Local codes specify minimum clearances (typically 5–6 meters for vehicular roads), and guardrails or crash barriers are installed below for protection. Lateral bracing ensures stability against wind loads. Expansion joints are often introduced before and after crossings to isolate structural movement. Erection over live roads poses safety and scheduling challenges, requiring detailed construction planning, permits, and often nighttime work to reduce disruption.
11. How do you address thermal bowing in long pipe runs supported on pipe racks?
Thermal bowing occurs when temperature gradients across the pipe cross-section cause uneven expansion, leading to bending or sagging. This is common in sunlight-exposed or cryogenic lines. To address this, insulation and cladding are uniformly applied to maintain even temperatures. Additional supports or guided hangers are provided at critical points. Pipe stress analysis includes bowing loads, and supports are placed to limit mid-span deflection. In some cases, the line is sloped or segmented to minimize the bowing effect. Materials with low thermal expansion coefficients may also be chosen for high-risk applications.
12. How do project execution models (EPC vs. EPCM) affect pipe rack design and delivery?
In an EPC (Engineering, Procurement, Construction) model, the contractor is responsible for all stages, ensuring tight integration and faster execution. Pipe rack design must be frozen early, with rapid procurement and fabrication. In contrast, EPCM (Engineering, Procurement, and Construction Management) allows more client oversight and flexibility, but may lead to slower decision-making and extended schedules. In EPCM, iterative feedback may require design revisions mid-way. Therefore, modular, adaptable designs are preferred. Project execution models affect communication flows, design timelines, and procurement strategies, which directly influence how pipe rack engineering and construction are managed.
13. What is the effect of creep and relaxation in high-temperature piping on pipe rack design?
Creep and relaxation occur in piping systems exposed to sustained high temperatures over time. Creep causes permanent deformation under constant load, while relaxation reduces stress in restrained systems. These effects can alter expected loads on supports and anchors, potentially leading to unplanned displacements or structural overstress. Pipe racks supporting high-temperature lines must use materials rated for long-term thermal exposure and account for potential dimensional changes in anchor and guide positions. Stress analysis includes time-dependent deformation predictions, and periodic inspection plans are developed to monitor deformation and integrity during the plant’s operational life.
14. How do you handle interdisciplinary load conflicts in shared pipe racks?
Interdisciplinary load conflicts arise when piping, electrical, HVAC, and instrument teams route systems through a common pipe rack without coordination. This may lead to overloading, insufficient space, or unbalanced load distribution. To mitigate this, a rack ownership model is defined, typically led by piping or structural teams. Shared 3D models, interface matrices, and regular coordination meetings are held. Loads are calculated with input from each discipline and verified through a centralized structural model. Load-sharing agreements and change control procedures help maintain clarity and accountability across teams, ensuring safe and optimized design.
15. What are the lifecycle considerations for maintaining structural integrity of pipe racks post-construction?
Post-construction, lifecycle maintenance includes periodic inspections for corrosion, structural fatigue, deformation, and damage from operational loads. Critical areas like baseplates, welds, bracings, and anchor bolts are visually and non-destructively tested. Inspection frequency is based on service conditions, environmental exposure, and regulatory requirements. Load re-evaluation is necessary when adding new lines or equipment. Digital twins and IoT sensors may be integrated for continuous monitoring. Maintenance strategies like recoating, bolt replacement, or structural retrofitting ensure extended service life. Documentation of all changes, inspections, and repairs ensures traceability and compliance with plant integrity management systems.
Course Schedule
Aug, 2025 | Weekdays | Mon-Fri | Enquire Now |
Weekend | Sat-Sun | Enquire Now | |
Sep, 2025 | Weekdays | Mon-Fri | Enquire Now |
Weekend | Sat-Sun | Enquire Now |
Related Courses
Related Articles
Related Interview
Related FAQ's
- Instructor-led Live Online Interactive Training
- Project Based Customized Learning
- Fast Track Training Program
- Self-paced learning
- In one-on-one training, you have the flexibility to choose the days, timings, and duration according to your preferences.
- We create a personalized training calendar based on your chosen schedule.
- Complete Live Online Interactive Training of the Course
- After Training Recorded Videos
- Session-wise Learning Material and notes for lifetime
- Practical & Assignments exercises
- Global Course Completion Certificate
- 24x7 after Training Support
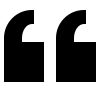