.jpg)
The SAP Logistics Execution (LE) Training equips learners with the skills to manage and streamline logistics operations within the SAP environment. It covers key components like delivery processing, transportation management, and warehouse integration. Participants will gain hands-on experience in handling goods movement, configuring shipping points, and optimizing shipment processes. This course is ideal for SAP end-users, consultants, and logistics professionals aiming to improve supply chain visibility and execution efficiency.
SAP Logistics Execution (LE) Training Interview Questions Answers - For Intermediate
1. What is the purpose of delivery split in SAP LE?
Delivery split occurs when multiple deliveries are created from a single sales order. This may happen due to factors like differing shipping points, delivery dates, or partial availability of stock. It helps in managing logistics flexibly and ensures timely shipment of available items.
2. How is transportation planning point different from a shipping point?
A transportation planning point is an organizational unit responsible for transportation processing, including shipment creation and cost calculation. A shipping point, on the other hand, is where goods are physically picked, packed, and dispatched. Both are essential but serve distinct purposes within logistics execution.
3. What triggers a goods receipt in inbound logistics?
A goods receipt is triggered when materials arrive at the receiving plant or warehouse. In SAP LE, it confirms that the products have been delivered as per the purchase order. It updates inventory and accounting records, marking the end of the inbound process.
4. What is the difference between inbound and outbound delivery?
An inbound delivery refers to receiving goods into the warehouse, typically from a vendor, while an outbound delivery handles shipping goods out to customers. Both types manage logistics processes, but in opposite directions of the supply chain.
5. How is warehouse management integrated into SAP LE?
Warehouse Management (WM) enhances LE by managing detailed warehouse processes such as bin-level inventory, transfer orders, and stock placements. When integrated with LE, it provides greater control over picking, packing, and goods movement at the warehouse level.
6. What is collective processing of deliveries?
Collective processing allows multiple deliveries to be processed together for tasks like picking, packing, or shipment creation. It improves operational efficiency, reduces redundancy, and supports batch processing through collective processing transactions in SAP.
7. How does SAP LE handle returns?
Returns in SAP LE are managed through return deliveries. Once a return order is created in SD or MM, a return delivery document is processed. It facilitates tracking, goods movement, and updates inventory and financials accordingly.
8. What are delivery blocks and how are they used?
Delivery blocks prevent delivery creation for specific sales or purchase orders. They are used for quality checks, credit limits, or approval workflows. This ensures that no delivery is processed until specific conditions are fulfilled.
9. What is the use of transportation groups in LE?
Transportation groups classify materials based on their transportation requirements, such as refrigeration or special handling. These groups are used during route determination and help plan appropriate transport resources.
10. How is proof of delivery handled in SAP LE?
Proof of delivery (POD) is a confirmation from the customer that goods were received in proper condition. SAP can capture POD data such as signature, date, or condition, and can be used to trigger invoicing or handle disputes.
11. What is the role of a route schedule in SAP LE?
A route schedule defines specific times and days a particular route is used. It automates planning and ensures that shipments align with transportation availability. It's especially helpful in recurring or predefined delivery cycles.
12. How does LE support third-party logistics (3PL) providers?
SAP LE supports integration with 3PL providers via EDI or interfaces. This allows external partners to receive delivery data, update shipment status, and send back confirmations, enabling seamless logistics operations even when outsourced.
13. What is the function of shipment stages in SAP?
Shipment stages break down the shipment process into steps like pre-carriage, main carriage, and on-carriage. Each stage can have its own mode of transport and timing. It provides detailed tracking and planning flexibility for complex logistics chains.
14. What are the steps involved in outbound delivery processing?
Outbound delivery processing typically involves delivery creation, picking, packing, goods issue, and shipment creation. Each step is tracked in SAP LE, and documents are updated accordingly to reflect inventory movement and customer fulfillment.
15. How can delivery priorities be set and used?
Delivery priorities are defined in the sales document and indicate the urgency of a delivery. SAP uses this data during delivery due list processing to decide which deliveries should be processed first, ensuring high-priority orders are fulfilled timely.
SAP Logistics Execution (LE) Training Interview Questions Answers- For Advanced
1. What is the significance of delivery document types in SAP LE, and how do they impact logistics processing?
Delivery document types in SAP LE define how a delivery behaves in the system, including its structure, allowed functions, and flow of processes. Each document type governs specific parameters such as whether it is an inbound or outbound delivery, what item categories are allowed, and which number range should be used. They also control whether the document can be relevant for shipment, billing, or warehouse management. By configuring different delivery types, organizations can handle diverse logistics scenarios like standard shipments, returns, stock transfers, or subcontracting deliveries. This helps ensure consistency in processing and enables tailored handling of various supply chain needs, enhancing operational accuracy and process control.
2. How do item categories function in SAP LE, and what role do they play in delivery processing?
Item categories in SAP LE determine how individual items within a delivery are treated, including whether they are relevant for picking, packing, goods movement, or billing. These categories are derived based on the delivery type and sales document item categories and allow for granular control over logistics execution. For example, an item category may indicate if the item is free of charge, needs to be packed, or should be batch-managed. They also define inventory posting behavior and influence the warehouse management requirements. Having correctly assigned item categories ensures that each material is handled as per business and compliance needs throughout the logistics process.
3. Explain the concept of transportation planning point and its relationship with shipment documents.
A transportation planning point is an organizational unit in SAP LE responsible for creating, planning, and monitoring shipment documents. It represents a logistics office or department where transportation planning activities such as shipment creation, cost calculation, and freight settlement are executed. Each shipment is assigned to a transportation planning point, and this association ensures accountability and segregation of duties, especially in decentralized logistics environments. The planning point controls access and visibility to shipment-related data, making it a critical component in aligning logistics operations with organizational structure and ensuring streamlined transportation activities.
4. What are the implications of incorrect goods issue posting in SAP LE, and how can they be corrected?
Incorrect goods issue posting can lead to discrepancies in stock, inaccurate accounting entries, and shipment tracking errors. It may result in the inventory being deducted wrongly, impacting availability checks and financial reports. To correct such errors, SAP allows reversal of goods issue, which resets the stock, financial documents, and delivery status. However, reversals must be managed carefully, especially if the documents are already integrated with billing or external systems. Audit trails, approval workflows, and proper user access control are essential to managing such corrections and maintaining data integrity within the logistics process.
5. How does SAP Event Management integrate with Logistics Execution, and what value does it add?
SAP Event Management (EM) integrates with SAP LE to provide real-time visibility into logistics processes by tracking predefined milestones, such as goods issue, shipment departure, or delivery receipt. EM receives event data from SAP or external systems and compares it with expected timelines. When deviations occur—like delayed pickup or early delivery—it triggers alerts for proactive resolution. This integration enhances supply chain transparency, supports exception-based management, and improves customer service through timely notifications. It is especially valuable in global or multi-leg transportation where delays or mishandling can affect delivery performance.
6. How do availability checks impact delivery creation in SAP LE?
During delivery creation, SAP performs an availability check to determine if the required quantity of a material is available in stock for picking and shipping. This check ensures that over-promising to customers is avoided and logistics resources are efficiently utilized. The system can use different types of ATP (Available-to-Promise) logic, considering current stock, planned receipts, safety stock, and reservations. If stock is insufficient, the system can either prevent delivery creation, suggest partial deliveries, or schedule later dates. Effective availability checking helps align warehouse operations with order fulfillment capabilities and improves customer satisfaction.
7. Discuss the role of condition records in shipment cost calculation within SAP LE.
Condition records in shipment cost calculation define how charges like freight, tolls, fuel surcharges, and carrier fees are computed for a shipment. These records are maintained using condition types and are stored in condition tables linked with access sequences. During shipment cost processing, the system uses these records to derive applicable charges based on parameters such as carrier, route, transportation zone, and shipment type. This allows for automated and consistent cost calculation, which is essential for accurate billing, cost control, and profitability analysis. Changes to condition records also offer flexibility in adapting to market rates or contractual changes.
8. What are packing instructions, and how do they improve logistics efficiency in SAP LE?
Packing instructions define rules for how materials should be packed into handling units, including packaging material types, quantities per unit, and nested packing requirements. They streamline the packing process by standardizing how items are grouped, reducing manual entry, and ensuring compliance with packaging norms. In SAP LE, packing instructions can be integrated with delivery processing to automate handling unit creation and label printing. This enhances warehouse efficiency, reduces packing time, and ensures accurate tracking of goods during transport. It's especially important for industries requiring standardized and regulatory-compliant packaging.
9. How does the warehouse number and storage location relationship affect SAP LE processes?
The warehouse number is used in Warehouse Management (WM) and EWM modules to represent a structured layout of bins and storage types, whereas the storage location represents a physical or logical subdivision within a plant. In SAP LE, the connection between delivery processing and WM/EWM is made via this relationship. When a delivery line item involves a storage location managed by WM, transfer requirements and transfer orders are automatically triggered. Incorrect mapping or missing configurations between warehouse numbers and storage locations can disrupt picking, stock updates, and goods issue, leading to logistical inefficiencies.
10. How does SAP LE support cross-docking, and what are its benefits?
Cross-docking in SAP LE enables direct transfer of goods from inbound to outbound delivery without long-term storage. It is especially useful in fast-moving goods environments like retail and perishable industries. SAP supports pre-planned and opportunistic cross-docking, where system-driven logic determines if incoming materials can directly fulfill outgoing delivery requirements. This reduces handling time, storage costs, and lead times. By integrating cross-docking logic into delivery and warehouse processes, SAP LE enables lean supply chain execution and improves turnaround efficiency.
11. What role does output determination play in the logistics execution process?
Output determination in SAP LE automates the generation and dispatch of logistics documents like delivery notes, packing lists, shipment notifications, and transport labels. It uses condition technique based on factors such as delivery type, shipping point, and customer. Proper configuration ensures that outputs are triggered at the right time and delivered through appropriate channels (print, email, EDI). Output determination ensures consistency, compliance with documentation requirements, and efficient communication with customers and logistics partners.
12. How does SAP LE support subcontracting processes through logistics?
In subcontracting scenarios, materials are sent to a vendor for processing, and logistics execution ensures timely delivery and receipt of goods. SAP LE handles outbound delivery of components to the vendor and inbound receipt of finished goods. It maintains transparency in inventory, tracks component consumption, and allows for batch traceability. Integration with MM and production modules ensures synchronized flow of materials and accurate accounting of logistics activities in subcontracting, which is vital for industries like automotive or electronics manufacturing.
13. What are the different picking strategies available in SAP LE, and how do they impact warehouse operations?
SAP LE supports several picking strategies including FIFO (First-In-First-Out), LIFO (Last-In-First-Out), shelf-life-based picking, and batch-based picking. These strategies help determine the sequence and priority in which items are retrieved from the warehouse. When integrated with Warehouse Management, SAP allows rule-based determination of storage bins and picking paths to optimize picker efficiency. Choosing the right picking strategy reduces inventory aging, supports regulatory compliance (like FEFO in pharma), and improves order fulfillment accuracy.
14. How can you handle partial deliveries and backorders in SAP LE?
Partial deliveries occur when full quantity is not available or not required at once. SAP allows configuration of delivery tolerance and partial delivery indicators at the customer or item level. For backorders, SAP LE enables rescheduling and monitoring through the backorder processing tool, which helps prioritize and confirm quantities for delayed deliveries. These features help manage inventory constraints, meet customer expectations, and maintain transparency on delivery commitments.
15. In what ways does SAP LE contribute to sustainability and green logistics initiatives?
SAP LE supports sustainability goals by enabling more efficient transportation planning, reducing fuel usage through optimized routes, and consolidating shipments. Handling unit management promotes reusable packaging tracking. Integration with SAP Environment, Health and Safety (EHS) module allows capturing emissions data and compliance with environmental regulations. By offering visibility into the entire logistics network, SAP LE empowers organizations to make data-driven decisions that reduce waste, minimize carbon footprint, and contribute to greener supply chain practices.
Course Schedule
Aug, 2025 | Weekdays | Mon-Fri | Enquire Now |
Weekend | Sat-Sun | Enquire Now | |
Sep, 2025 | Weekdays | Mon-Fri | Enquire Now |
Weekend | Sat-Sun | Enquire Now |
Related Courses
Related Articles
Related Interview
- AVEVA Instrumentation Administrator Interview Questions Answers
- Plant Design using CADWorx Plant Professional Training Interview Questions Answers
- AVEVA P&ID Administration Interview Questions Answers
- IBM Platform LSF Advanced Administration and Configuration for Linux (H023G) Training Interview Questions Answers
- Salesforce Health Cloud Training Interview Questions Answers
Related FAQ's
- Instructor-led Live Online Interactive Training
- Project Based Customized Learning
- Fast Track Training Program
- Self-paced learning
- In one-on-one training, you have the flexibility to choose the days, timings, and duration according to your preferences.
- We create a personalized training calendar based on your chosen schedule.
- Complete Live Online Interactive Training of the Course
- After Training Recorded Videos
- Session-wise Learning Material and notes for lifetime
- Practical & Assignments exercises
- Global Course Completion Certificate
- 24x7 after Training Support
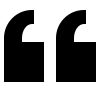