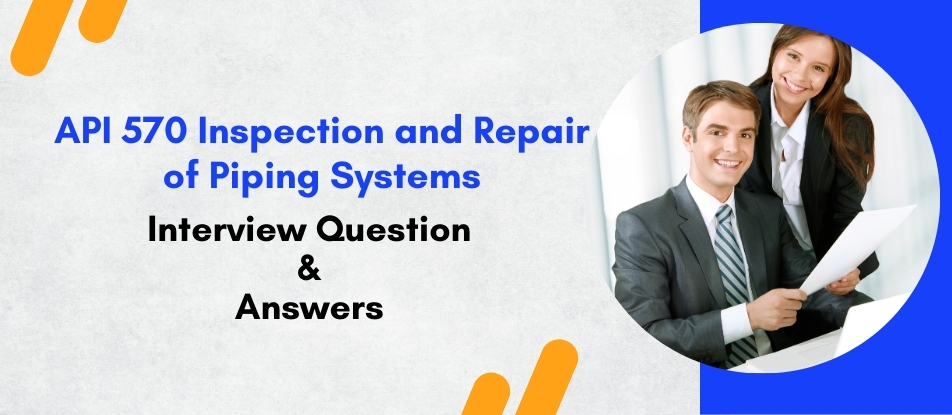
API 570 Inspection and Repair of Piping Systems training equips professionals with the knowledge to inspect, evaluate, and maintain in-service piping systems. The course covers inspection codes, corrosion assessment, repair procedures, and fitness-for-service principles. It emphasizes safety, compliance, and best practices in petrochemical and process industries. Ideal for aspiring inspectors, engineers, and maintenance personnel, it prepares candidates for the API 570 certification and enhances their ability to manage piping system integrity efficiently.
API 570 Inspection and Repair of Piping Systems Training Interview Questions Answers - For Intermediate
1. What is the scope of API 570?
API 570 covers the in-service inspection, repair, alteration, and rerating activities for metallic piping systems. It applies primarily to petroleum refineries, chemical plants, and related industries, ensuring the integrity and safety of piping during operation.
2. What are the main responsibilities of an API 570 inspector?
An API 570 inspector is responsible for conducting inspections, evaluating piping conditions, ensuring compliance with codes, recommending repairs, and verifying that piping remains safe for continued operation. They also maintain documentation and support risk-based inspection planning.
3. How often should a piping inspection be conducted?
Inspection frequencies are determined based on factors like corrosion rate, damage mechanisms, service conditions, and prior history. Typically, external visual inspections occur every 5 years or less, while internal or on-stream inspections depend on calculated remaining life.
4. What is the difference between a major and a minor repair under API 570?
A major repair affects the pressure boundary or requires welding that alters the original design, needing engineering approval. A minor repair is simpler, like replacing gaskets or valves, and may not require formal design calculations or re-rating.
5. What is meant by corrosion rate, and how is it calculated?
Corrosion rate is the rate at which metal is lost due to chemical or electrochemical reactions. It's calculated using thickness measurements over time with the formula:
(T1 - T2) / Time Interval, where T1 and T2 are the previous and current thicknesses respectively.
6. Explain the term “minimum required thickness” (tmin).
Tmin is the minimum wall thickness that a piping component must have to safely contain the internal pressure under specific conditions. It’s determined through design equations and includes allowances for corrosion and mechanical loads.
7. What are common damage mechanisms affecting piping systems?
Common damage mechanisms include general corrosion, pitting, erosion, stress corrosion cracking, hydrogen-induced cracking, and mechanical fatigue. Understanding these helps in selecting appropriate inspection methods and determining remaining life.
8. How is Risk-Based Inspection (RBI) used in API 570?
RBI is used to prioritize inspections based on the risk posed by failure of piping components. It considers the probability of failure and the consequence of failure, allowing for optimized inspection intervals and resource allocation.
9. What is a CUI and why is it critical?
Corrosion Under Insulation (CUI) is a type of corrosion that occurs when moisture infiltrates thermal insulation. It’s critical because it can remain hidden, leading to undetected wall thinning and sudden failures.
10. What is the role of Non-Destructive Examination (NDE) in API 570?
NDE techniques like UT (Ultrasonic Testing), RT (Radiographic Testing), and MT (Magnetic Particle Testing) are vital for detecting flaws without damaging the piping. They support inspectors in evaluating wall thickness, weld quality, and hidden defects.
11. When is rerating of a piping system required?
Rerating is required when process conditions change—like pressure or temperature—or when extensive repairs or replacements are made. It involves recalculating allowable stress and ensuring the system meets new operating parameters.
12. What documentation must be maintained according to API 570?
Documents include inspection reports, thickness monitoring data, repair records, engineering calculations for rerating, and updated piping drawings. Maintaining accurate records ensures traceability and supports regulatory compliance.
13. What considerations are made for weld repairs in piping?
Weld repairs should follow ASME B31.3 and be approved by authorized engineers. Considerations include proper welding procedures, qualifications, preheat requirements, post-weld heat treatment, and NDE to confirm weld integrity.
14. What are typical causes of premature piping failure?
Premature failures may arise from poor maintenance, inadequate inspection, material defects, improper design, or unforeseen damage mechanisms. Early detection and proactive measures are critical to preventing incidents.
15. What does the term “Fitness-for-Service” (FFS) mean in the context of API 570?
FFS is an assessment methodology used to determine if a component can continue to operate safely with known defects. It evaluates remaining strength, possible failure modes, and provides repair or mitigation options.
API 570 Inspection and Repair of Piping Systems Training Interview Questions Answers - For Advanced
1. How does API 570 address the concept of corrosion loops, and how are they different from circuits?
Corrosion loops are conceptual groupings of piping that experience similar degradation mechanisms, based on process conditions and fluid characteristics. While often used interchangeably with “circuits,” loops focus more on damage mechanisms (e.g., sulfidation, chloride stress corrosion cracking) than just physical layout or materials. API 570 emphasizes the importance of corrosion loops in risk-based inspection (RBI) planning because they allow inspectors to classify components more accurately for degradation monitoring. By analyzing corrosion loops, a facility can optimize CML placement, standardize inspection intervals, and apply predictive analytics more effectively.
2. What are the common causes of vibration-induced fatigue in piping systems, and how are they identified?
Vibration-induced fatigue occurs due to cyclic stresses from flow-induced vibration, mechanical resonance, or pulsation in process piping. Common causes include unsupported spans, pump vibrations, reciprocating compressors, and turbulence at flow changes. Symptoms such as cracked welds, noise, or failures at branch connections often indicate fatigue. Identifying these requires vibration analysis, dynamic stress calculations, and field observation. Techniques such as strain gauges and modal analysis are used for advanced diagnosis. Proper support design, damping systems, and routine vibration monitoring help mitigate this issue.
3. Discuss how material selection impacts inspection planning under API 570.
Material selection directly influences corrosion susceptibility, damage mechanisms, and inspection methods. For instance, carbon steel is vulnerable to general corrosion and CUI, requiring regular thickness monitoring and insulation removal. Austenitic stainless steels may resist general corrosion but are prone to chloride stress corrosion cracking, necessitating specialized inspection like dye penetrant testing. High-temperature alloys may undergo creep damage, needing replication or metallographic analysis. Understanding material behavior under operational environments enables better inspection scheduling and targeted techniques, aligning with API 570’s goal of predictive and preventive maintenance.
4. What are the critical considerations in developing an effective piping inspection program for high-temperature services?
High-temperature piping systems face unique challenges, including creep, thermal fatigue, oxidation, and stress-assisted corrosion. An effective inspection program considers temperature profiles, thermal cycles, material creep limits, and weld heat-affected zones. Regular monitoring of creep-prone areas with techniques like metallographic replication and hardness testing is essential. Expansion joints, supports, and insulation integrity should also be inspected, as their failure can exacerbate damage. API 570 provides guidance on integrating these assessments into a comprehensive strategy that aligns with operational safety and reliability goals.
5. How do you manage temporary repairs in piping systems, and what are the limitations?
Temporary repairs such as clamps, enclosures, or wraps may be used in emergencies but must be approved by qualified engineers and documented thoroughly. These repairs are designed for short-term service until permanent solutions can be applied. API 570 specifies that temporary repairs should be monitored frequently and not relied upon beyond the approved period. Limitations include reduced pressure containment, potential stress concentrations, and lack of long-term reliability. Permanent repair plans must be scheduled promptly, and fitness-for-service evaluations are often required to justify continued operation.
6. Explain the importance of inspection isometrics in a piping inspection program.
Inspection isometrics are annotated piping diagrams used to document CMLs, inspection findings, corrosion rates, and other critical information. They provide a visual reference that simplifies data interpretation, supports traceability, and facilitates communication across engineering, maintenance, and inspection teams. These drawings are continuously updated to reflect changes in CML locations, damage mechanisms, and repair history. Effective use of isometrics ensures alignment with API 570’s requirement for accurate and current documentation of piping condition and inspection results.
7. What are the advantages and challenges of applying acoustic emission (AE) testing in piping systems?
AE testing detects stress-induced energy releases, such as crack growth or corrosion, by capturing acoustic signals during pressurization. Advantages include real-time monitoring, wide area coverage, and minimal disruption to operations. AE is especially effective in detecting active damage mechanisms. However, challenges include signal interpretation complexity, noise interference, and the need for skilled analysts. It is not a replacement for UT or RT but a supplementary tool in specific cases like high-pressure systems or composite repairs.
8. What are the steps to establish a corrosion control document (CCD), and why is it important?
A Corrosion Control Document (CCD) outlines expected corrosion mechanisms, control strategies, and inspection requirements for process systems. Steps include identifying materials and fluids, analyzing operating conditions, consulting process flow diagrams (PFDs), and reviewing failure history. It documents corrosion rates, critical circuits, and mitigation plans such as inhibitors or coatings. CCDs provide a framework for developing RBI plans and inspection intervals, ensuring alignment between operations, maintenance, and inspection. API 570 encourages CCD use to enhance proactive corrosion management.
9. How is ultrasonic phased array testing different from conventional UT, and when is it preferred?
Phased array ultrasonic testing (PAUT) uses multiple transducer elements with programmable delays to steer and focus sound waves. Compared to conventional UT, PAUT offers enhanced resolution, faster scanning, and better defect characterization. It can generate cross-sectional images of welds and corroded areas, making it ideal for complex geometries and critical joints. It is preferred in weld inspection, corrosion profiling, and fitness-for-service assessments where detailed visualization and high accuracy are required. However, it demands skilled technicians and specialized equipment.
10. What are the common root causes of wall thinning in piping, and how are they systematically addressed?
Wall thinning arises from corrosion, erosion, or a combination of both, often due to turbulent flow, improper metallurgy, or chemical attack. Common areas include elbows, reducers, and downstream of control valves. Systematic addressing involves identifying damage mechanisms, modifying process parameters, adding erosion-resistant linings, or altering piping design. Predictive monitoring with thickness trending and proactive replacement planning is critical. API 570 requires establishing acceptable thickness limits and applying RBI or FFS methods to determine safe operation thresholds.
11. What is the significance of stress intensification factors (SIFs) in API 570 assessments?
SIFs are multipliers used in stress analysis to account for increased stresses at geometric discontinuities like tees, elbows, and branch connections. They are vital in flexibility analysis and fatigue evaluations. In API 570, SIFs influence decisions related to rerating, FFS evaluations, and determining the criticality of welds or components. Incorrect estimation can lead to under- or over-design and misjudged inspection priorities.
12. How does hydrogen-induced cracking (HIC) manifest in carbon steel piping, and how is it detected?
HIC is a type of damage where atomic hydrogen diffuses into steel and forms internal cracks, often in sour service environments. It typically manifests as stepwise or blister-like cracking parallel to the surface. Detection requires specialized techniques such as ultrasonic backscatter or Time-of-Flight Diffraction (TOFD). HIC can compromise toughness and lead to catastrophic failure if undetected. API 570 inspectors must understand its risk factors—such as hydrogen sulfide (H2S) presence, steel quality, and wet conditions—and monitor susceptible systems accordingly.
13. What key parameters are considered in developing an effective pressure test plan?
A pressure test plan includes selection of test fluid (usually water or inert gas), test pressure (typically 1.5 times design pressure for hydrotests), hold time, temperature considerations, and safety precautions. The plan should specify test boundaries, isolation requirements, instrumentation calibration, and leak detection methods. Documentation, such as test procedures and permits, must be prepared in compliance with jurisdictional codes. API 570 emphasizes that testing should not overstress components, especially older systems, and alternatives like NDE should be considered where hydrotests pose risks.
14. Describe how API 570 ensures mechanical integrity in systems exposed to cyclic service.
Cyclic service, such as batch operations or temperature-pressure fluctuations, can cause fatigue damage over time. API 570 addresses mechanical integrity by requiring increased inspection frequencies and detailed tracking of damage accumulation. Components like elbows, supports, and welds are monitored for early signs of cracking or distortion. RBI may consider the number of cycles in its risk calculation, and advanced techniques like fracture mechanics are used in FFS assessments. Ensuring flexible supports, proper design, and timely inspection are crucial in such environments.
15. How are inspection records structured and maintained according to API 570?
Inspection records must include equipment identification, inspection dates, methods used, findings, measured thicknesses, corrosion rates, remaining life, recommendations, and actions taken. They should be traceable, well-organized, and updated after each inspection or repair. API 570 recommends using computerized inspection databases that support trending and RBI integration. Records must be retained for the life of the piping system, ensuring regulatory compliance and historical reference. A well-maintained record system enables efficient audits, risk evaluation, and planning of future inspections.
Course Schedule
Aug, 2025 | Weekdays | Mon-Fri | Enquire Now |
Weekend | Sat-Sun | Enquire Now | |
Sep, 2025 | Weekdays | Mon-Fri | Enquire Now |
Weekend | Sat-Sun | Enquire Now |
Related Courses
Related Articles
- What is the difference between SAP APO and SAP IBP? - SAP IBP Online Training Course
- Most Trending Primavera Interview Questions & Answers
- Safeguarding Your Digital Fortress: A Guide to CyberArk Training
- 8 Reasons Why STAAD.Pro v8i Online Course Should Be Your Next Career Move
- Benefits of SP3D Electrical Certification
Related Interview
Related FAQ's
- Instructor-led Live Online Interactive Training
- Project Based Customized Learning
- Fast Track Training Program
- Self-paced learning
- In one-on-one training, you have the flexibility to choose the days, timings, and duration according to your preferences.
- We create a personalized training calendar based on your chosen schedule.
- Complete Live Online Interactive Training of the Course
- After Training Recorded Videos
- Session-wise Learning Material and notes for lifetime
- Practical & Assignments exercises
- Global Course Completion Certificate
- 24x7 after Training Support
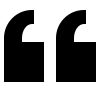