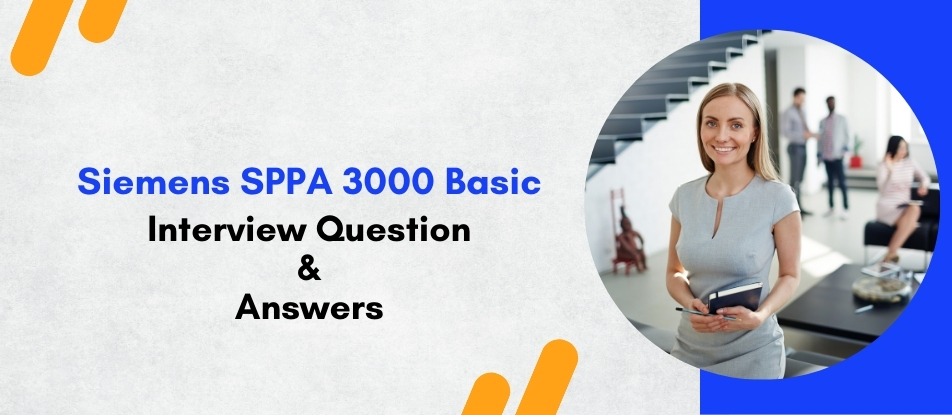
The Siemens SPPA-T3000 Basic Training program equips professionals with foundational knowledge of SPPA-T3000 DCS used in modern power plants. Participants learn system components, web-based interface navigation, control logic development using CFC/SFC, alarm handling, diagnostics, and engineering workflows. Ideal for control engineers and operators, the course builds practical skills for configuring, operating, and maintaining SPPA-T3000 systems, ensuring reliability, scalability, and seamless integration within critical plant environments.
Siemens SPPA 3000 Basic Training Interview Questions Answers - For Intermediate
1. What is the primary purpose of the Process Object View in SPPA-T3000?
The Process Object View (POV) is used to provide an operator-centric view of the plant’s process hierarchy. It offers easy navigation between different control and monitoring elements, allowing users to access alarms, trends, and real-time data efficiently from a single location.
2. How does SPPA-T3000 handle software updates without plant downtime?
SPPA-T3000 supports online engineering and hot-swappable updates, meaning software or configuration changes can be made and deployed without shutting down the system. This ensures continuous plant operations and reduces downtime for maintenance tasks.
3. What is the role of the I/O controller in SPPA-T3000?
The I/O controller interfaces with field devices and transmits signals to and from the automation server. It converts physical input/output signals into digital data that the control system can process and use for real-time operations.
4. Explain the significance of function blocks in control configuration.
Function blocks are reusable logic modules in the CFC editor that simplify control configuration. Engineers can build complex control strategies by linking multiple blocks, making development modular, scalable, and easier to maintain.
5. What is the difference between engineering mode and runtime mode in SPPA-T3000?
Engineering mode is used for creating and modifying control logic, HMI screens, and configurations, while runtime mode is for live monitoring and operation. Changes made in engineering mode can be tested and activated without affecting the running system.
6. Describe the data archiving capability in SPPA-T3000.
SPPA-T3000 supports long-term data archiving for operational logs, trends, and alarms. This data can be exported for analysis, compliance reporting, or predictive maintenance, contributing to improved plant reliability and regulatory adherence.
7. What is the purpose of the SPPA-T3000 Web Workplace?
The Web Workplace is a browser-based interface that provides access to the DCS for both engineers and operators. It enables monitoring, control, and configuration from standard PCs without the need for dedicated software installation.
8. How is user management handled in SPPA-T3000?
User management is based on role-based access control. Administrators can assign users different permissions—such as view-only, operator, or engineer—ensuring that only authorized personnel can perform sensitive operations or modifications.
9. What are the benefits of object-oriented engineering in SPPA-T3000?
Object-oriented engineering enables the reuse of templates and standardized components, reducing engineering time and minimizing errors. This approach promotes consistency across plant systems and simplifies maintenance and upgrades.
10. Explain the concept of signal tracing in SPPA-T3000.
Signal tracing allows engineers to follow the flow of a signal from the field device through the I/O controller and logic blocks to the operator interface. It is a powerful troubleshooting tool that helps locate faults and verify configurations.
11. How does SPPA-T3000 manage communication between components?
The system uses an Ethernet-based network architecture for communication. Redundant networks and protocols like TCP/IP ensure secure, fast, and reliable data exchange between servers, clients, and field devices.
12. What is the purpose of the runtime database in SPPA-T3000?
The runtime database stores all operational parameters, logic states, and process values. It ensures real-time performance and is continuously updated to reflect current plant conditions for both control and monitoring purposes.
13. How is redundancy implemented at the server level in SPPA-T3000?
Redundancy is achieved by running two servers—primary and backup—in parallel. In case the primary server fails, the backup seamlessly takes over operations without disrupting plant functionality or data availability.
14. What diagnostic features are available for identifying control system faults?
SPPA-T3000 provides detailed diagnostics through visual indicators, error logs, trend analysis, and alert notifications. Engineers can quickly identify hardware or software faults and perform corrective actions to maintain system stability.
15. How are graphics and HMI elements configured in SPPA-T3000?
The system offers a graphical editor where engineers can design operator displays using drag-and-drop elements. These displays show real-time data, alarms, and control buttons, providing intuitive process visualization for plant personnel.
Siemens SPPA 3000 Basic Training Interview Questions Answers - For Advanced
1. How does SPPA-T3000 support the concept of virtual commissioning, and what are its advantages in power plant projects?
SPPA-T3000 supports virtual commissioning through simulation tools that replicate the control logic, I/O signals, and operator interfaces in a fully virtualized environment. Engineers can test automation logic, validate sequences, and train operators without actual hardware deployment. This reduces on-site commissioning time, mitigates project risks, and helps identify errors early in the development cycle. Virtual commissioning also allows for stakeholder engagement, as project teams can visualize and interact with the system prior to go-live. In highly regulated and mission-critical environments like power generation, this approach significantly enhances system reliability and safety during actual commissioning.
2. Explain the scalability of SPPA-T3000 and how it supports small units to large fleet-wide deployments.
SPPA-T3000 is inherently scalable, thanks to its modular architecture and centralized server-client model. Whether it's a small gas turbine or a large utility-scale thermal plant, SPPA-T3000 can be configured to suit the plant size and complexity. It allows the addition of controllers, servers, and clients as needed without disrupting existing operations. Moreover, multiple units across a fleet can be managed under a unified engineering and monitoring framework, supporting centralized diagnostics, remote access, and multi-site standardization. This scalability supports phased rollouts and investment protection as plants expand or modernize over time.
3. What are the data integrity mechanisms in SPPA-T3000, especially in high-availability environments?
SPPA-T3000 ensures data integrity through real-time synchronization of control and application servers, buffered communication for I/O data, and validation mechanisms in engineering tools. Time-stamped data is archived with millisecond accuracy, ensuring precise historical analysis. The system includes checksum verification, automatic recovery after network glitches, and mirrored databases to prevent data loss. For high-availability environments, redundant paths and watchdog mechanisms continuously verify data transmission health and automatically trigger fallback modes if inconsistencies are detected, preserving both real-time control and historical accuracy.
4. How does SPPA-T3000 contribute to predictive maintenance in modern power plants?
SPPA-T3000 collects vast amounts of real-time operational and condition monitoring data, which is essential for predictive maintenance. It integrates seamlessly with diagnostic tools, vibration analysis systems, and historian platforms. By analyzing trends and deviations from baseline performance, it identifies early signs of equipment wear, potential failure, or inefficiency. Predictive maintenance minimizes unplanned downtime, optimizes spare part inventory, and improves asset lifespan. SPPA-T3000’s compatibility with AI-powered analytics tools further enhances its predictive capabilities, enabling maintenance to be scheduled based on actual usage and condition rather than fixed intervals.
5. How are safety instrumented systems (SIS) integrated or interfaced with SPPA-T3000?
While SPPA-T3000 itself is not a Safety Instrumented System, it interfaces with SIS units using standard communication protocols such as Profibus or OPC. Safety-related logic is handled in certified separate hardware systems, and SPPA-T3000 monitors their statuses, diagnostic data, and alarm states. Visualization of SIS functions can be done through operator displays, but control and override capabilities remain segregated per safety regulations. This layered safety architecture ensures compliance with IEC 61511 standards, promoting functional safety and minimizing the risk of human error in critical environments.
6. Describe how the SPPA-T3000 system supports time synchronization across distributed components.
Time synchronization is critical in SPPA-T3000 for consistent logging, diagnostics, and control accuracy. The system uses Network Time Protocol (NTP) to synchronize all devices—including servers, clients, I/O modules, and controllers—with a common time reference. A master time server, often linked to a GPS clock, ensures nanosecond-level synchronization across the plant. This is especially important for event sequencing, post-event analysis, and synchronized operation between redundant systems. The accuracy and reliability of time sync also enable compliance with industry standards and forensic analysis in incident investigations.
7. How does SPPA-T3000 handle load shedding and black-start conditions in a power plant?
SPPA-T3000 includes built-in functions for load shedding based on pre-defined priorities, frequency drops, and power generation constraints. During grid disturbances or black-start situations, it automatically reduces non-critical loads and sequences power restoration through SFC-based logic. The system coordinates with turbine and generator controllers to ensure safe ramp-up and synchronization. Visual feedback to operators, integrated alarms, and event logs enable fast decision-making and smooth recovery. This ability is vital for grid stability and ensuring the plant can respond effectively during emergencies or island-mode operations.
8. What are the HMI capabilities in SPPA-T3000 and how do they enhance operator efficiency?
SPPA-T3000's HMI is entirely web-based and customizable. It supports advanced graphics, animated elements, multiview dashboards, and alarm navigation. Operators can drill down from overview displays to detail levels, access trends, and control loops with minimal clicks. High-performance HMI design principles—such as color-coded alerts, consistent layouts, and dynamic links—improve response time and reduce cognitive load. Additionally, the system supports touchscreens, dual monitors, and mobile/tablet access, enabling flexible control room layouts and operator mobility.
9. How are performance optimization strategies supported by SPPA-T3000 analytics and reporting features?
SPPA-T3000 includes real-time and historical performance monitoring for key plant KPIs like efficiency, fuel usage, emissions, and heat rates. It offers customizable reports and dashboards for different stakeholders. Data can be exported or integrated with external analytics platforms for in-depth modeling. Engineers use this data for tuning PID loops, optimizing setpoints, and benchmarking unit performance. With integrated OEE (Overall Equipment Effectiveness) indicators and real-time alerts, plant personnel can proactively identify bottlenecks or underperforming units.
10. How is training and simulation implemented using SPPA-T3000 environments?
Training simulators based on SPPA-T3000 use the same engineering and HMI environment as the live plant, offering a realistic operator training experience. Simulated I/O and virtual process models allow personnel to practice startups, shutdowns, and emergency procedures without risking equipment. These simulators can be synchronized with actual control logic and updated as the plant evolves. Siemens also supports training scenarios and logging of trainee actions for assessment, ensuring knowledge retention and readiness for real-life operations.
11. Discuss the importance and structure of diagnostic buffering in SPPA-T3000.
Diagnostic buffering in SPPA-T3000 involves collecting system and process events, status changes, and error codes in time-ordered logs that can be retained even during communication outages. These buffers help engineers analyze the root cause of events, especially after a system reboot or failover. Events are stored locally and synchronized with the central database once communication is restored. This ensures no diagnostic information is lost and supports accurate post-event reviews, fault isolation, and reporting.
12. How does SPPA-T3000 assist with environmental compliance and emission reporting?
SPPA-T3000 tracks and logs critical emission data such as NOx, SOx, CO2, and particulate levels. It supports continuous emissions monitoring system (CEMS) integration and can be configured to generate regulatory reports in formats required by environmental agencies. Data integrity and traceability are ensured through time stamps, secure logging, and audit trails. Alarms and trends related to emission limits allow real-time operator intervention, helping maintain compliance with local and international environmental standards.
13. How is network redundancy and segregation managed in SPPA-T3000 installations?
Network redundancy in SPPA-T3000 is managed via redundant Ethernet rings, VLANs, and dual-port NICs. Control and business networks are segregated through firewalls or physically separate infrastructures. Critical data flows, such as I/O communications and HMI updates, are prioritized using QoS settings. The system supports automatic switchover in case of network failures and logs each switch event. This architecture ensures uninterrupted data flow and meets the reliability needs of power plants while protecting against cyber and physical network failures.
14. Describe how the lifecycle of instrumentation and I/O modules is managed through SPPA-T3000.
SPPA-T3000 maintains an integrated asset management database where each I/O point and field device is catalogued with tags, calibration dates, diagnostics, and maintenance history. The system can generate alerts for overdue calibrations, out-of-range values, and device wear. Engineers can run diagnostic routines directly from the HMI, reducing the need for field intervention. Device templates and libraries ensure consistency in configuration and documentation, supporting predictive maintenance and easy replacement strategies.
15. How can SPPA-T3000 be prepared for future integrations like AI, IIoT, and cloud platforms?
SPPA-T3000 is built on open standards and modular architecture, making it future-ready. Siemens provides secure APIs, OPC UA support, and connectors for cloud platforms such as MindSphere or Azure. These integrations allow data exchange with AI and ML engines for predictive analytics, anomaly detection, and smart recommendations. The system supports containerized applications and edge computing devices that bring intelligence closer to the process. Combined with Siemens' ongoing digitalization roadmap, SPPA-T3000 is positioned to serve as the central nervous system for the smart power plant of the future.
Course Schedule
Aug, 2025 | Weekdays | Mon-Fri | Enquire Now |
Weekend | Sat-Sun | Enquire Now | |
Sep, 2025 | Weekdays | Mon-Fri | Enquire Now |
Weekend | Sat-Sun | Enquire Now |
Related Courses
Related Articles
Related Interview
Related FAQ's
- Instructor-led Live Online Interactive Training
- Project Based Customized Learning
- Fast Track Training Program
- Self-paced learning
- In one-on-one training, you have the flexibility to choose the days, timings, and duration according to your preferences.
- We create a personalized training calendar based on your chosen schedule.
- Complete Live Online Interactive Training of the Course
- After Training Recorded Videos
- Session-wise Learning Material and notes for lifetime
- Practical & Assignments exercises
- Global Course Completion Certificate
- 24x7 after Training Support
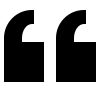