This Machine Vision Systems course provides a comprehensive understanding of image processing, object detection, and automated inspection techniques used in industrial environments. Learners gain hands-on experience with cameras, lighting setups, vision software, and system calibration. The course also explores advanced topics like 3D vision, deep learning integration, and vision-guided robotics, preparing professionals to develop reliable, real-time visual inspection solutions for manufacturing, packaging, automotive, and quality assurance industries.
Machine Vision Systems Training Interview Questions Answers - For Intermediate
1. What is thresholding in machine vision, and when is it used?
Thresholding is an image segmentation technique that converts grayscale images into binary images based on a specific pixel intensity value. It helps in separating objects from the background, simplifying the detection of shapes, edges, and features. It's commonly used in applications like blob analysis, defect detection, and presence/absence verification.
2. How does blob analysis help in machine vision?
Blob analysis is used to detect and measure connected regions (blobs) in a binary image. It allows the system to extract information such as area, centroid, orientation, and bounding box of objects. This technique is valuable for counting items, checking alignment, and identifying faulty or missing components.
3. What are the types of lenses used in machine vision systems?
Common lenses include fixed focal length lenses, zoom lenses, telecentric lenses, and macro lenses. Fixed lenses are used in stable setups, zoom lenses offer flexibility, and telecentric lenses maintain consistent magnification without perspective distortion—critical for precision measurement tasks.
4. Explain the concept of Field of View (FOV) and Depth of Field (DOF).
FOV is the area visible through the camera lens, determining how much of the object can be captured. DOF refers to the range within which the object remains in acceptable focus. Proper configuration of both ensures that critical features are captured sharply and entirely within the frame.
5. What is the purpose of using filters in machine vision?
Optical filters are used to control the wavelength of light reaching the camera sensor. They help eliminate unwanted reflections, enhance contrast, and isolate specific colors. For instance, infrared filters are useful in low-light conditions, while polarizing filters reduce glare from shiny surfaces.
6. How do barcodes and QR codes get read by vision systems?
Machine vision systems use pattern recognition and decoding algorithms to read 1D barcodes and 2D codes like QR codes. The camera captures the code, and the vision software deciphers the encoded information. Proper lighting and image resolution are key for accurate decoding.
7. What is image stitching, and where is it applied?
Image stitching combines multiple overlapping images to create a single, wide-field or high-resolution image. It is useful in inspecting large objects or surfaces that cannot be captured in a single frame, such as PCB panels, solar cells, or flat sheets.
8. How does motion blur affect machine vision and how can it be prevented?
Motion blur occurs when an object moves during image capture, causing a smeared appearance that hampers analysis. It can be minimized by using faster shutter speeds, increasing light intensity, or employing strobe lighting. Triggered capture methods also help by syncing image acquisition with object movement.
9. What is the role of frame grabbers in a vision system?
Frame grabbers are hardware interfaces that capture image data from industrial cameras and pass it to the processing unit. They are essential for high-speed, high-resolution applications where real-time processing and deterministic performance are needed, especially in multi-camera setups.
10. Describe a typical vision system integration workflow.
Integration begins with defining requirements, followed by selecting appropriate hardware (camera, lens, lighting). Next is designing the software workflow—image acquisition, preprocessing, feature extraction, and decision-making logic. The final step is system calibration and integration with automation systems like PLCs or robots for control actions.
11. What is gray-scale morphology in image processing?
Gray-scale morphology extends binary morphology operations like erosion and dilation to grayscale images. It helps in enhancing structures, reducing noise, and separating touching objects. These techniques are particularly helpful in complex texture or shading scenarios common in industrial inspections.
12. How are neural networks applied in modern machine vision systems?
Neural networks, especially convolutional neural networks (CNNs), are used in vision systems for advanced tasks like defect classification, object detection, and anomaly recognition. These models learn from large image datasets and outperform rule-based systems in scenarios with variable conditions or subtle defects.
13. What is a Region of Interest (ROI), and why is it used?
An ROI is a user-defined subset of an image selected for focused analysis. Processing only the ROI reduces computational load and improves speed. It is particularly useful when only certain areas of the image contain relevant data or features for inspection.
14. Explain the concept of perspective distortion in machine vision.
Perspective distortion occurs when objects closer to the lens appear larger than those farther away, affecting accuracy in measurements. It can be mitigated using telecentric lenses or applying geometric corrections via camera calibration and image transformation algorithms.
15. How do you validate a machine vision system after deployment?
Validation involves testing the system against a set of known conditions and defect scenarios. This includes checking image acquisition consistency, algorithm accuracy, false positives/negatives, and integration with automation systems. Statistical performance measures like accuracy, precision, and repeatability are used to ensure reliability.
Machine Vision Systems Training Interview Questions Answers - For Advanced
1. How do FPGA and GPU accelerators differ in accelerating machine-vision workloads, and what factors guide the choice between them?
Both FPGAs and GPUs can slash inference times, but they excel in different scenarios. FPGAs deliver deterministic, microsecond-scale latency thanks to their deep pipelining and hard-wired logic, making them ideal for ultra-high-speed inspection lines or when tight, repeatable timing is mandatory (e.g., print registration at >20 kHz). They also draw less power per operation once configured. GPUs, by contrast, offer massive parallelism with thousands of streaming cores and a mature CUDA/OpenCL ecosystem, enabling rapid prototyping and frequent re-training of deep networks. They shine when running large CNNs or when model updates are weekly rather than once per quarter. Selection hinges on latency budget, power envelope, required model agility, engineering skill sets (HDL vs. CUDA/Python), and total cost of ownership—including toolchain licenses and time-to-market.
2. What technical challenges arise when synchronizing multi-camera arrays for 360° or line-scan inspections, and how are they mitigated?
Multi-camera arrays must capture frames within microseconds of one another to avoid motion parallax or stitching artifacts. Jitter from asynchronous triggers, cable delays, and drift between camera oscillators can lead to blurred seams or dimensional errors. Mitigation begins with a hardware global-start trigger via TTL, LVDS, or IEEE-1588 PTP to lock time bases. Deterministic networking (Time-Sensitive Networking, TSN) keeps packet latency bounded on GigE Vision systems. Further, master-slave clock topologies or shared crystal oscillators can maintain sub-nanosecond alignment. In high-speed web inspection, encoder-based position triggers synchronize exposure to product motion, while overlapping FOVs and on-the-fly homography correction in the vision software eliminate residual mis-registration.
3. Why might an engineer deploy a real-time operating system (RTOS) for a vision controller, and what trade-offs does this introduce?
An RTOS such as QNX, VxWorks, or RT-Linux guarantees bounded task scheduling latency—critical when the vision controller must latch inspection results and actuate a reject gate within a few milliseconds. Hard real-time guarantees avoid sporadic garbage-collection pauses common in general-purpose OSs. However, RTOS adoption increases development overhead: driver availability is limited, third-party libraries require cross-compilation, and UI frameworks may be rudimentary. Teams must weigh the cost of deterministic behavior against engineering complexity; sometimes a carefully tuned Ubuntu-PREEMPT_RT kernel suffices, especially if the vision cycle time is >10 ms and network jitter is the dominant factor.
4. How can domain adaptation techniques reduce re-training effort when a vision model is moved to a new production line with different lighting and backgrounds?
Domain adaptation leverages shared representations between source (trained) and target (new) domains. Techniques like adversarial feature alignment (e.g., DANN), style transfer augmentation, or batch-normalization statistics recalibration can make a model lighting-agnostic without full re-labeling. Practically, a small set of unlabeled target images passes through a domain discriminator that forces intermediate features to be indistinguishable from the source distribution. Alternatively, few-shot fine-tuning with self-supervised pretext tasks (contrastive learning) adapts the encoder while freezing the task-specific head. This cuts annotation time dramatically—often from thousands of images to a few dozen—and speeds deployment to satellite factories.
5. Discuss the role of photorealistic synthetic data in training deep-learning vision systems and the key pitfalls to avoid.
Synthetic data generated via tools like Blender, Unity, or NVIDIA Omniverse can cover rare defect modes, extreme poses, and exhaustive lighting permutations impossible to photograph. When domain randomization is applied—varying textures, colors, and noise—the network learns invariant features and often transfers well to real parts. Yet, the “sim-to-real gap” looms: if rendered images lack realistic sensor noise, lens blur, or spectral reflectance, models over-fit to synthetic crispness and fail on noisy factory feeds. Incorporating physically based rendering (PBR), adding Poisson noise, and blending a small percentage of real images in mixed-batch training help close this gap. Continuous validation on live line data remains indispensable.
6. How do inline X-ray or computed-tomography (CT) vision systems differ from optical systems in design and data processing?
Inline X-ray/CT systems visualize internal structures, enabling solder-joint void analysis or cast-metal porosity detection unreachable by optics. Design constraints include radiation shielding, detector scintillator efficiency, conveyor thickness limits, and avoidance of motion blur at low photon flux. Reconstruction algorithms (e.g., filtered back-projection or iterative algebraic techniques) demand GPU or FPGA acceleration to achieve sub-second cycle times. Image preprocessing involves beam-hardening correction, ring-artifact removal, and 3D segmentation of volumetric defects. Data sizes explode—hundreds of megabytes per part—necessitating on-the-fly ROI cropping and edge analytics to compress results into pass/fail metadata before archiving.
7. Describe how machine-vision data feeds predictive-maintenance models in smart factories.
Vision metrics such as defect frequency, edge sharpness degradation, or histogram shifts act as leading indicators of tool wear, lens contamination, or lighting decay. By streaming these KPIs to an IIoT platform, time-series models—ARIMA, Prophet, or LSTM—forecast when inspection performance will drift beyond SPC limits. Coupled with maintenance logs, a causal relationship emerges: e.g., rising blur correlates with spindle vibration. Predictive dashboards then schedule lens cleaning or lamp replacement before quality escapes occur. This closed loop elevates vision systems from mere inspectors to health sensors for the entire line.
8. In collaborative robot cells, how does vision contribute to safety while maintaining throughput?
Vision-based safety systems employ stereo or LiDAR cameras creating dynamic safety zones: if an operator’s limb encroaches, the robot slows (power-and-force limiting) or stops. Unlike fixed light curtains, vision zones adapt to tool pose, maximizing reachable workspace without compromising standards like ISO 10218-1. Advanced AI segmentation distinguishes humans from foreground parts, reducing false alarms. Latency must remain <100 ms, demanding edge inference on certified safety-rated processors. Integrating safety PLCs with SIL 3 documentation ensures functional safety compliance while sustaining 20+ cycles per minute.
9. What cybersecurity threats target networked machine-vision systems, and how can they be mitigated?
Threat actors may inject spoofed images, altering inspection outcomes, or exploit outdated GigE Vision firmware to pivot into OT networks. Deepfake defect injections could trigger unnecessary scrap. Countermeasures include TLS-encrypted image streams, cryptographic hash signing of firmware, network segmentation with firewalls, and zero-trust authentication for remote debugging. Runtime anomaly detection monitors packet patterns; abrupt bitrate spikes trigger isolation. Security patches must be validated against real-time performance to avoid latency regressions.
10. How do standards like EMVA 1288 and ISO 17266 facilitate objective benchmarking of vision components?
EMVA 1288 defines sensor performance metrics—quantum efficiency, temporal dark noise, dynamic range—measured under strict conditions, allowing apples-to-apples comparison across camera vendors. ISO 17266 covers end-to-end machine-vision measurement systems, specifying test artifacts, calibration procedures, and uncertainty budgets. Adhering to these standards streamlines supplier qualification and regulatory audits, providing traceable documentation that the system meets metrological requirements. It also enables predictive modeling of inspection capability (gauge R&R) before capital expenditure.
11. Explain how simultaneous localization and mapping (SLAM) benefits autonomous mobile inspection robots in warehouses.
SLAM combines onboard vision (stereo or RGB-D) with inertial measurements to build a real-time 3D map while estimating the robot’s pose. In warehouses, SLAM allows inspection bots to navigate aisles, capture SKU barcodes, and check shelf integrity without GPS. Vision-based loop-closure detection eliminates cumulative drift, ensuring positional accuracy <5 cm over hundreds of meters. Dynamic obstacle detection and path-replanning maintain safety around forklifts. Integration with warehouse management systems lets robots update inventory discrepancies instantly.
12. How are transparent or specular materials inspected, given that conventional vision struggles with reflections?
Techniques include retro-reflective lighting, polarization imaging, and coaxial coax up-light to minimize glare. Fringe projection or differential phase-shift deflectometry measures micro-surface deviations even on mirror-like surfaces. UV fluorescence additives or laser scatter can reveal embedded cracks in glass. Some systems exploit short-wave infrared (SWIR) where glass becomes opaque, allowing internal structure visualization. Combining multiple modalities—e.g., polarized visible plus SWIR—fuses complementary information, yielding robust inspection despite challenging optics.
13. What advantages do event-based (neuromorphic) cameras bring to high-speed inspection, and what limitations exist?
Event cameras output asynchronous pixel-level intensity changes at microsecond latency, producing sparse data streams ideal for tracking ultra-fast objects like solder droplets. They avoid motion blur and cut bandwidth by orders of magnitude compared to frame-based cameras. Algorithms must shift from frame-centric CNNs to spiking neural networks or voxelized event tensors, which are still maturing. Low light and stationary-scene detection remain challenging because event output ceases without motion, necessitating hybrid architectures with conventional sensors.
14. How is latency budgeting performed in an end-to-end vision-controlled reject system?
Engineers break the pipeline into acquisition (exposure + readout), transfer (interface latency), processing (CPU/GPU/FPGA), decision logic, and actuator drive time. Each segment is profiled with logic analyzers or packet sniffers. Safety margin (typically 10–20 %) accounts for worst-case variances. If total exceeds the mechanical reject window (travel distance ÷ line speed), mitigation might include dropping resolution, applying region-of-interest cropping, or relocating the inspection station upstream to extend actuation lead time. Continuous monitoring with histograms of cycle-time distribution verifies budget adherence.
15. Compare pure edge, pure cloud, and hybrid edge-cloud architectures for vision analytics in terms of latency, scalability, and data sovereignty.
Pure edge performs inference and decision-making locally, minimizing latency (<50 ms) and easing data-sovereignty concerns but limiting model complexity to on-prem hardware. Pure cloud centralizes heavy analytics, enabling fleet-wide learning and elastic compute, yet suffers 100-300 ms WAN delays and raises compliance issues (GDPR, export controls). Hybrid edge-cloud splits the workload: the edge executes real-time passes/fails while streaming compressed metadata and periodic raw frames to the cloud for deeper trend analysis and re-training. This achieves sub-100 ms control latency, scalable model updates, and regional data-residency compliance by anonymizing or encrypting sensitive imagery before upload.
Course Schedule
Aug, 2025 | Weekdays | Mon-Fri | Enquire Now |
Weekend | Sat-Sun | Enquire Now | |
Sep, 2025 | Weekdays | Mon-Fri | Enquire Now |
Weekend | Sat-Sun | Enquire Now |
Related Courses
Related Articles
Related Interview
- Distributed Control System (DCS) Training Interview Questions Answers
- SAP Liquid UI Training Interview Questions Answers
- Primavera P6 Advanced Training Interview Questions Answers
- DP-203 Data Engineering on Microsoft Azure Interview Questions Answers
- Salesforce Certified Platform Developer I Training Interview Questions Answers
Related FAQ's
- Instructor-led Live Online Interactive Training
- Project Based Customized Learning
- Fast Track Training Program
- Self-paced learning
- In one-on-one training, you have the flexibility to choose the days, timings, and duration according to your preferences.
- We create a personalized training calendar based on your chosen schedule.
- Complete Live Online Interactive Training of the Course
- After Training Recorded Videos
- Session-wise Learning Material and notes for lifetime
- Practical & Assignments exercises
- Global Course Completion Certificate
- 24x7 after Training Support
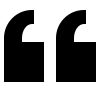